This is my transporter camper conversion blog. Its my first conversion and I started in September 2010.
Wednesday 30 November 2011
More Sound Proofing
Sorry for the delays in updating the blog. I have been beavering away on more modifications to the van and only now am I finding the time to put some words and pictures online.
Regular readers will know that I am keen on making the van as sound proof as possible so that the driving experience is more luxury car than panel van. My latest focus has been to add insulation to the kitchen units, the engine bay and some other areas of the cabin.
![]() |
Adding backs to the cupboards |
![]() |
preparing the panels for the foam insulation |
This was a fairly straight forward exercise using some open cell foam I bought in a job lot from ebay. I simply cut the panels to size and then used some spray adhesive to secure the foam to the rear of the panels
![]() |
foam attached |
Another area of focus was the engine bay. I decided to use some closed cell foam here to ensure that it didn't absorb moisture or oil. The material was purchased from ebay and came with a sticky back, so it was a simple job of cutting, peeling and sticking.
attaching to the underneath of the bonnet |
Foam as delivered |
![]() |
under tray before cleaning |
under tray after cleaning |
under tray with soundproofing |
The last area of focus was the cab floor. This is a slightly longer task as you have to remove the seats. WARNING: please remember do this exercise on flat ground with the wheels chocked as when you remove the driver seat you have to remove the hand brake.
Once the seats were removed the flooring was also pulled up and flash band was applied to the entire floor area. Refitting the rubber carpet was a nightmare job, most probably because I didn't remove the lower plastic panel from underneath the gear stick..... (learn from my mistakes!)
![]() |
Passenger seat removed |
Thursday 18 August 2011
Sound proofing - an obsession illustrated with pictures!
Having spent a lot of time sound proofing the back of the van earlier on in the project my attention turned to the cab area. I used by iphone to identify areas of high noise (db meter app) and decided that a good start would be the dashboard.
The general guidance with any sound insulation is that the first step is to block sound and the second step is to absorb the sound. With this in mind I diassembled the dashboard as much as I could by taking off all of the access panels and by removing the glove box. Having done this I then added flash band tape to the plat surfaces to reduce resonance and provide some absorption for the high frequency noise.
While the panels were removed I used some synthetic fibre wool to fill the voids behind the dashboard to provide some sound absorption.
After replacing the glovebox I lined the inside of it with flashband tape.
This item is the tray from the top of the dash, as you can see I added flashband tape to lower its resonant frequency and to provide some damping.
I stuffed this cavity full of wool, taking care not to interfere with the electrical harnesses and steering system.
Sound system
Its been a while since I have updated what I have been doing. I have been doing quite a lot... so here goes.
Heres a view of the interior withe seat fitted. Its amazing when I look back at the humble plumbers van I first purchased in August 2009 and see what can be achieved with a bit of elbow grease!
I decided that the sound system fitted in the van was no where near good enought so I went to Loughborough and purchased a new Alpine CD single DIN and a set of 4 'fly' speakers to replace the standard door speakers and also to install into the rear of the van.
Fitting the fly speakers in the doors was pretty straight forward. I purchased the appropriate adaptors and they simply dropped in. I connected them up via the supplier crossover system and hey presto all was done.
I decided that the 6*9s would work best mounted in the rear seat/bed base and so set about cutting the apertures to fit them. This was a really straightforward job as the speakers came with the appropriate templates.
Heres a finished speaker. I was quite pleased with the result.
I will add a better picture of the interior in due course.
Sunday 22 May 2011
Interior moves on
I have been very busy beavering away on the van over the last month ticking off small jobs here and there and getting the cushions sorted. I finished off the bed box at the front and carpeted it to make it look neater and fit in with the rest of the van.
![]() |
fitting the seat kick board |
This area would also serve as useful storage and a place to fit some extra speakers.
![]() |
seat kick board fitted |
There it is finished and ready to be carpeted. I used 6mm ply for this, its likely that I will go around all of the 6mm ply areas and sound deaden with flash band or maybe some proprietary material. The thinner play does lend itself to booming which I do not want!
interior looking nearly finished |
Here's a few of the interior on our 'shakedown' camping trip to the peak district. The van is by no means finished yet so we were able to create a snag list of things to tackle next.
Tuesday 26 April 2011
Interior Build Part 3 - fitting the sink into the worktop
A campervan is not really a campervan unless it has a sink. I decided upon a SMEV unit which I sourced via ebay. It has two gas burners and a sink and came with a tap that actuates the pump electrically upon operation. The quality of the item is good, the only issue is that no template is supplied to allow you to work out what size/shape of a hole to cut out for it ! I got around this by tracing the outline of the whole thing and then measuring in from the line appropriately and then using those points to describe the appropriate profile.
A bit of jigsawing later and the hole was cut. The next step was to cut down into the wall between the cupboards to allow for the depth of the sink and gas fittings.
Tadah! the unit fitted perfectly. I decided not to use the SMEV fixing method which involved a completely inpractical arrangement of oddly shaped fixing points, instead I opted for silicone... I may live to regret it but several hundred miles later and its absolutely fine.
Tuesday 19 April 2011
The interior build part 3
With the units installed and fixed the next step was to finish off the bed platform and to begin fitting the doors to the cabinets. I decided to get up early again and have good days worth of work progressing to my goal of using the van at the easter bank holiday.
So heres where I left the the bed platform at. As mentioned previously the goal now was to make it stiffer laterally.
To achieve this a piece of 9mm ply was cut and the bottom left hand corner scribed and jigsawed to fit the contour of the van.
By now I had got quite adept at scribing and the piece fitted first time, perfectly!
I then set about marking out and then cutting the aperture to enable the area to be used for storage. The eagle eyed amongst you will have spotted that the other side of the bed platform had been finished also. the result of fitting the both of these panels was that the whole structure became incredibly stiff, a quick test with me trying to move it with my body weight proved this!
The interior build Part 2
With the bed platform given a jumpstart due to teamwork between myself, my Dad and my Mam the next weekend was set for further leaps forward. The weather was also getting much better and bank holidays approaching fast - I decided to up the ante. This particular weekend I decided to be up and working on the van by 8am...
I was keen to get started on the other elements of the kitchen install and as mentioned previously this meant a trip to Ikea to get the units and doors. I decided that this weekend that I would work in the courtyard of my apartment building (it was a lovely day).
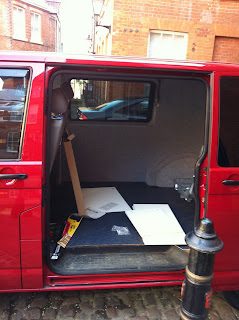
The first job was to build all the units. Ikea units are pretty straightforward to put together, if a little boring! Its quickly done and then I started the job of adapting the units to fit the contours of the vehicle.
It is important to treat the collection of units as one unit during this fitting process. What you will find if you decide to follow a similar path is that you have to space the units a little bit out from the wall to ensure you compensate for the curve in towards the roof of the vehicle. I suggest that you build all the units up, fix the position along the length of the vehicle before starting your scribing exercise.
Next was to tackle the top unit at the rear. This was a little more tricky to get right as there are two dimensions that you need to scribe in.
I was keen to get started on the other elements of the kitchen install and as mentioned previously this meant a trip to Ikea to get the units and doors. I decided that this weekend that I would work in the courtyard of my apartment building (it was a lovely day).
In order to get the contours correct I used the 'scribing' technique which was passed from Father to Son in the recent bed platform build. This enabled me to , relatively quickly, get the cabinets cut to fit over the wheel arch and to fit into the rear portion, near the doors.
It is important to treat the collection of units as one unit during this fitting process. What you will find if you decide to follow a similar path is that you have to space the units a little bit out from the wall to ensure you compensate for the curve in towards the roof of the vehicle. I suggest that you build all the units up, fix the position along the length of the vehicle before starting your scribing exercise.
After not too long an the use of a jigsaw I got the units to fit very nicely. I was very pleased with myself at this stage!
Heres where I got to by the end of the day. Units were all in and I fixed them to the floor using screws into the ply and used a collection of brackets to fix to the walls. A good days work.
The interior build Part 1
I've been quiet for a few weeks online but that doesn't mean I haven't been busy. I have been concentrating on the interior build. I had been researching the best way to do this for some time and I came to the conclusion that I would attempt an 'Ikea Build'. The reason for this choice is that I wanted to have a clean look and I decided that the extra weight (20-30kg) over a custom lightweight ply approach was a penalty I was willing to live with.
Here you can see the arrangement of the side panels as described above. We started by bracketing this support in place. A large set square was necessary as you can't really rely on a spirit level in a vehicle....
You would have seen from previous posts that I had already purchased a Volkswares rock 'n' roll bed. This meant that I would have to build the rear of the bed - this was the first thing that I focused on. I picked a weekend when my Dad would be around as he is a very handy gentleman with wood and other practical things AND, of course, I enjoy working with him!
I decided that we would work outside my brothers house. It was a relatively fine day (there was a brief shower) and the tools that I needed were all within easy reach.
Here's what we started with. I had removed the bed to give space but had previously worked out how long, high and wide the platform needed to be.
A trip to local builders merchant (Wickes) was needed to assemble the materials. I chose a 9mm ply and some 30x40mm battens for the supports and cross members.
Here's my dad, smiling, he loves his son's projects :-)
A quick double check on the beds location was needed to ensure we got it right first time. (Measure twice, cut once etc...... I've learnt my lessons!)
I had prepared the side panels separately so we had a bit of a head start. The side panels were made from a 12mm MDF panels with battens glued and screwed on the top edge.
Here you can see the arrangement of the side panels as described above. We started by bracketing this support in place. A large set square was necessary as you can't really rely on a spirit level in a vehicle....
Naturally Dad got to work in following my instructions... hah hah!
We also fitted some vertical supports to take load down into the floor.
These were screwed in place to the side panels and then the side panel was bracketed to the floor.
The same was repeated on the other side of the van and four cross members were fitted to take the weight of the two adults that could be on the platform at any one time.
Even my Mam decided to get involved at this point. The next step was to work on the platform lid itself, this was made from two layers, a layer of 12mm MDF roughly shaped to the contours of the van followed by a more accurately shaped 9mm ply sheet.
This top sheet was screwed multiple times to the structure beneath leading to a very strong structure in the vertical plane. What it lacks at this stage is any kind of triangulation to prevent lozenging - this is covered later.
As you can see it is currently an open structure that will provide a lot of storage space underneath.
At this point we left it as it was starting to rain and we had a deadline to meet with a family meal to attend.
Subscribe to:
Posts (Atom)